Typing for long hours with intermittent breaks is the ethos of my job description, but do it for a few years, and a few realizations start to dawn. For one, the short breaks aren't quite enough to relieve the physical strain on your back, wrists, and eyes. It didn't take me long to prioritize ergonomics in my desk setup so I could put in longer hours. However, I've noticed several peers treating desk comfort as an afterthought to basic functionality. I chose to give it equal importance as my obsession with mechanical keyboards and their comfortable typing experience set me up for several side quests, like matching custom cables, keycaps, and wrist rests.
While there are plenty of options for cables and keycaps, I noticed that a vast majority of heavy typists and gamers rely on a simple wooden plank, sometimes molded or infused with resin, as a keyboard wrist rest. I followed suit and tried using one, but gave up in frustration after a year. Thus began a journey to create custom wrist rests, leveraging my expertise in CAD and the revolution in ease of access to affordable and reliable 3D printing and scanning.
4 Cushion and support are different things
There's a good reason why planks are so popular
Microsoft's guide to desk ergonomics suggests sitting with your elbows perpendicular and arms in front of you, while your wrists hover over the keyboard to facilitate movement and typing. Trying to implement this firsthand quickly proves it is untenable for long stints without gravity playing a role and eventually pulling your wrist down to sit atop your desk, lower than the keyboard.
As a mere mortal, I too succumbed to gravity and typed with my wrists, sharing the surface on which my keyboard and mouse sat. It seemed comfortable in the short term, but after a few hours of typing stretched into days, I was acquainted with the term "wrist extension" and the associated physical pain. Keeping your wrist extended to reach keys, combined with the typical inward twisting or pronation of the wrist, is an ergonomic disaster. Some argue that using the flip-out feet on your keyboard to raise the upper rows increases wrist extension instead of making typing more comfortable.
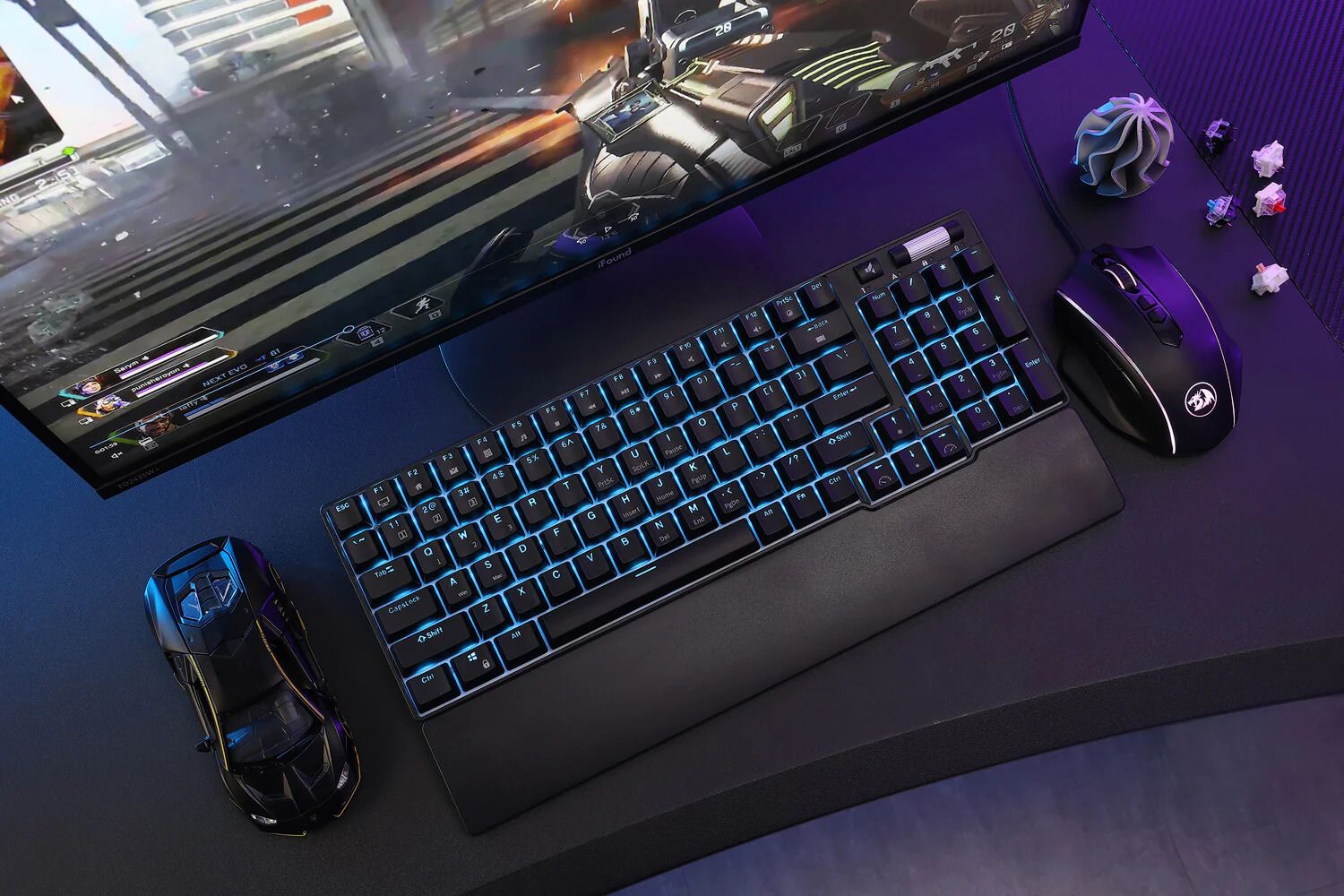
This is when I bought a wooden plank barely thicker than my keyboard so that I could rest my wrists. I ruled out squishy wrist rests and desk mats with integrated gel pockets. Sooner than later, they would sag or collapse under the weight of my resting wrists, defeating their fundamental purpose of raising the wrist. The plank was like a rudimentary splint for a bandaged fracture, but it was quite comfortable, and I used it for almost a year until a couple of frustrations boiled over. First, the wrist rest was immobile, so I still had to lift my hand instead of sliding it over it to reach for, say, the numpad. Second, this convenience did not extend to my mouse, since I'm not a trackball user. So, my wrist continued to hurt from using mice without a dedicated rest.
3 Drawing inspiration from professional gaming gear
And creating an unabashed yet unique clone
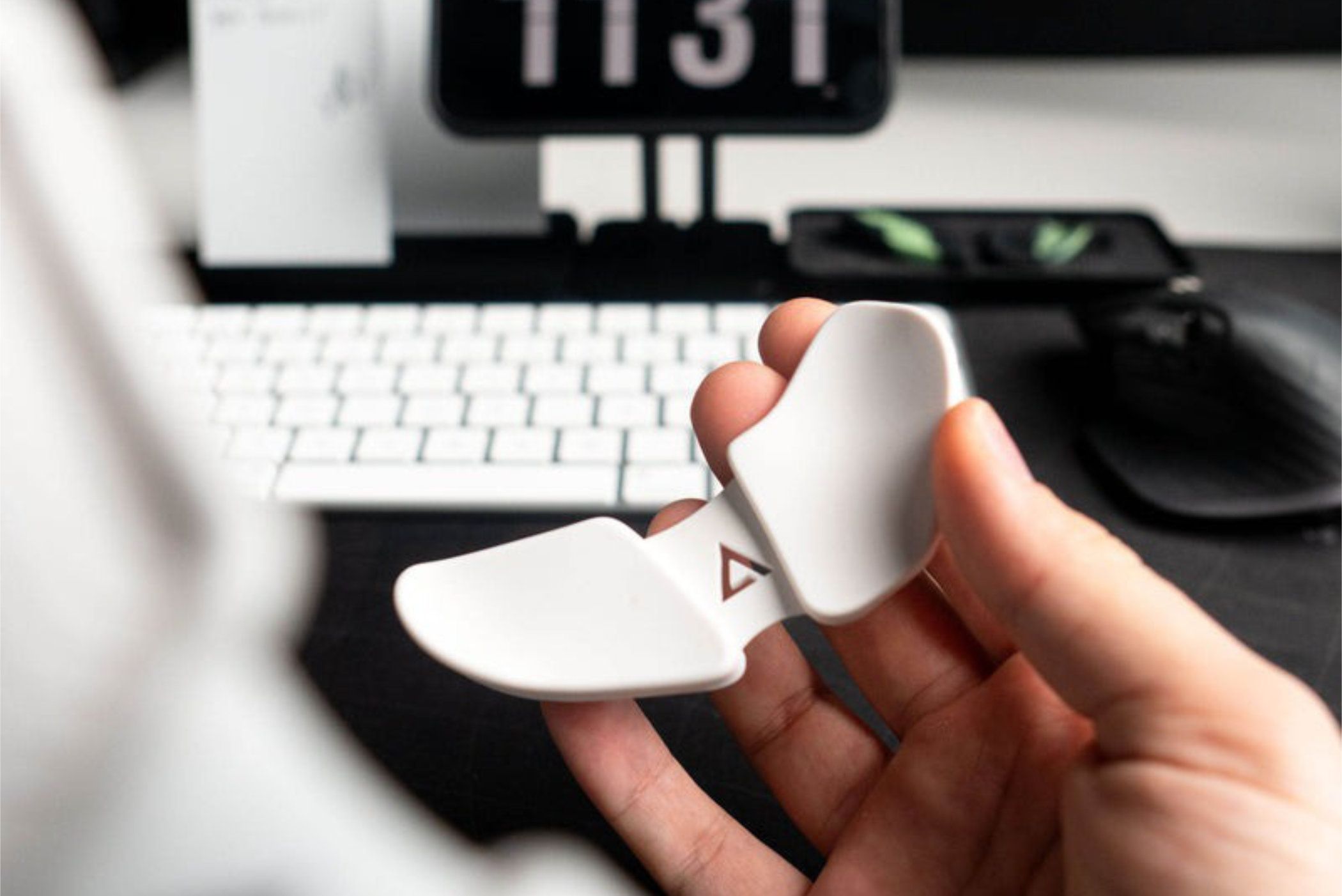
Source: Deltahub
The inspiration: Deltahub Carpio
My dissatisfaction prompted me to delve deeper into variations of wrist rests, just as I started shrinking my keyboard, so I didn't need to stray too far from the home row to begin with. I found the Deltahub Carpio and several other similarly shaped, sculpted rests advertised for usage even with mice. These products are mostly aimed at gamers who need comfort and the freedom of rapid mouse movement. They shared the general idea that you could move your hand without lifting it off the rest, since the rest would move in tandem, gliding on Teflon feet just like your mouse. Most designers for this product seemed convinced that the peaks and valleys of the sculpted upper would create enough friction with your hand, so the wrist rest doesn't break free.
With the Carpio unavailable locally, I bought a similarly sculpted plastic rest with a detachable unibody cushion made of soft-touch plastic. It wasn't squishy or grippy, and as a result, I found my wrist unceremoniously dethroned from its perch when moving the mouse around rapidly. Moreover, buying the left and right-handed versions so I could substitute my wooden wrist rest with this contraption proved frustrating because it was too short for comfort, and my wrist was still extending. This was the final nail in the coffin.
Left to right: Compiling scans in Meshroom; Meshroom output; Topographical map of my wrist impression; Initial designs with flat cushions and subsequent iterations
My academic background in mechanical engineering, design, and production stirred awake as I set about loosely replicating these commercially available Deltahub Carpio knockoffs, albeit without the limitations I found. Around this time, I also found a heavily used first-generation Deltahub Carpio for additional R&D.
I started by taking an impression of my right wrist in air-drying clay, which I used with mouse feet underneath as a proof of concept. It was heavy, but showed promise. So, I 3D scanned it using an Android app called Polycam and then refined and patched the mesh in MeshLab before importing and scaling it down to the correct size in Siemens NX, a CAD software. Besides the usual objectives when designing a 3D printable model, such as minimizing filament consumption, the need for support structures, and print time, my primary objectives for the design were:
- A fully 3D printable output
- Fully modular components with inter-compatibility between different versions
- Design for backwards compatibility with future revisions
- Sufficient room for customization
- Replaceable and firm cushions
2 3D printing comes in clutch
A new product takes shape
Subsequent iterations of the design with raised inner cushions and mirrored halves
After dozens of hours spent designing and refining the product in CAD software, I got my first 3D printout. Typically, my design efforts would have been in vain, since most other manufacturing processes are reserved for the deepest pockets or those with familiarity and access to industrial machinery. However, in the past decade, 3D printing has pervaded everything from university labs to hobbyist workbenches, and I could not be happier. Printing in plastic is a great way to reduce effort and materials spent prototyping, all while reducing the downtime between iterations to fine-tune the design.
I called my third iteration a finished product — a wrist rest for either hand, custom sculpted to fit my wrist, with enough tractive force from the layer lines in the print so it wouldn't fly out from underneath. I used PLA plastic as a base, Tiger Ice and X-RayPad Jade mouse skates, and 85A Shore hardness TPU for the cushions. These cushions are slightly larger than their receptacles, leveraging the squishiness of TPU to press-fit in place. This simplifies replacement once worn out, and offers slightly cushioned support without collapsing under the weight of my hands. Additionally, the layer lines from FDM printing automatically create a sufficiently textured surface that eliminates the grip issues I alluded to earlier.
The cushions are replaceable and the emote on the base can be changed too, with layer lines for sufficient grip
Besides iterating to find the optimal print infill densities, wall thicknesses, and placement of the mouse feet, I also sought input from doctors specializing in this field. Their critical advice shaped the design with suggestions, such as raising the inner cushion for either wrist rest above the outer one. While the height delta doesn't make a difference to the typing experience, it reduces the scissoring of the forearm bones, a phenomenon known as pronation of the wrist—making typing more comfortable than if your entire wrist were resting on the same flat surface (like wood). I also rounded the corners of the cushions to make the design friendlier for other people using my computer.
From a customization standpoint, I could now mix and match any color of PLA for the base with any color of TPU cushion to perfectly match my keycaps and custom coiled cable. I went a step further and designed a second PLA base slightly shorter than the original, to use with low-profile keyboards like the Lofree Edge, which have been gaining in popularity. In the two years since I've designed this, I have worn through three sets of cushions used on an assortment of bases.
1 Functional improvements galore
There's more that's better than just the looks
The custom solution is great for use with split keyboards
While ready access to desktop 3D printing and scanning enabled significant cosmetic and ergonomic improvement over a plank of wood wrist rest, this new product fundamentally changed how I use my keyboard. Previously, my wrists would hover near the keyboard with the forearm planted on the chair's armrests, but would eventually tire out and slouch down to sit on the wooden rest until I needed to reach a distant key.
With the wrist rest I've conceptualized, I don't need to lift my wrists up at all. I can just slide my hand across the desk mat to reach any end of the keyboard. The visual clutter on my desk has also been reduced since there's very little unused surface area on the wrist rest. I've found the unique split design also comes in handy when I switch to a split keyboard or an Alice/Arisu layout. Moreover, these wrist rests are significantly lighter and smaller, so I tend to throw a pair in my travel bag if I'm traveling with my keyboard.
3D Printing offers more if you go beyond downloading models
There is nothing wrong with downloading a printable model from the interwebs, keying in the recommended print settings, and hitting Print on your machine. Several kind souls have created a thriving community of free designs after investing tons of their time and effort to dial the results in. However, if you're getting into 3D printing, I simply urge that you learn to use design tools somewhere down the road. I believe that if hobbyists are willing to experiment and learn mechatronics through 3D printing, learning to use new software should be a relative walk in the park.
Acquiring even basic design skills unlocks one half of the joys of 3D printing: realizing that something you thought up can translate into a tangible product after a few hours of design work. With 3D scanning becoming more affordable and accessible through smartphone apps, replicating objects or printing repair and replacement tools is now easier than ever.